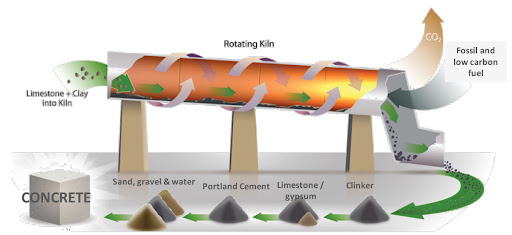
How cement and concrete are made?
Cement is the basic element in concrete. It is a delicate powder that serves as the glue that keeps concrete together during mixing with water, sand, and aggregates.
Cement is made by burning a precise mixture of finely crushed limestone, clay, and sand in a rotating oven to temperatures approaching 1450ºC. This occurs in the generation of cement clinker, a standard product in the production of cement. The cement clinker covers from the kiln are reduced, and when finely crushed to compose the powder we understand it as cement. The fuels combusted to burn the kiln tale for about 40% of cement-producing discharges. The resting 60% are “process discharges”. when limestone is superheated, it delivers its carbon atoms and sorts CO2 in the kiln — which are completely fundamental.
Cement is just a tiny part of the method for concrete, typically improving up only around 7% to 10% of the concrete mixes. The additional basic elements of concrete are sand, gravel (fine and coarse aggregate), and water.
Elements — called admixtures — are seldom added while the concrete making stage to ambush air, remove water, increase the viscosity, and develop other special properties. Producers improve the bonding method of cement at the concrete production step with additional cementing materials (SCMs), which appear from manufacturing waste streams.
The core elements of cement (limestone, sand, and clay) and concrete (cement mixed with sand, gravel, and water) are between the most generally free raw materials on Earth. Portland cement is the primary component of concrete. Concrete is produced when Portland cement produces a glue with water that joints with sand and rock to harden.
Read More: What is the difference between Portland cement and Quikrete?
Cement is produced through a jointly controlled chemical compound of calcium, silicon, aluminum, iron, and other components. Natural materials used to produce cement combine limestone, shells, and chalk or marl merged with shale, clay, slate, blast furnace slag, silica sand, and iron ore. Those ingredients, when burned at high temperatures produce a rock-like material that is ground into the fine powder that we commonly think of as cement.
Bricklayer Joseph Aspdin of Leeds, England first assigned portland cement advanced in the 19th century by lighting powdered limestone and clay in his kitchen oven. With this rough method, he placed the reason for an industry that yearly processes mountains of limestone, clay, cement rock, and other elements into a powder so narrow it will pass within a sieve fitted of existing water. Cement plant labs verify each step in the production of portland cement by various chemical and physical experiments. The labs also examine and test the complete product to assure that it complies with all business terms.
The most common way to produce portland cement is within a dry method. The initial step is to quarry the primary raw materials, essentially limestone, clay, and other elements. After quarrying, the stone is smashed. This includes several steps. The first crushing reduces the rock to a maximum volume of around 6 inches. The rock then proceeds to secondary crushers or hammer mills for the decrease to about 3 inches or shorter. The crushed rock is blended with other elements such as alloy ore or fly ash and ground, mixed, and fed to a cement kiln.
The cement kiln fires all the elements to about 2,700 degrees in huge cylindrical steel rotary kilns filled with proper firebrick. Kilns are usually as much as 12 feet in width—large sufficient to support an automobile and higher in many situations than the maximum of a 40-story structure. The large kilns are attached with the axis twisted slightly from the parallel.
The finely ground raw metal or the slurry is filled into the more expensive end. In the lower end is a roaring blast of fire, composed by precisely managed burning of powdered coal, oil, alternative fuels, or gas below-forced selection.
What is cement made of?
As we understand, cement is the main ingredient used to make concrete. But cement isn’t any sort of generally occurring natural material – it’s produced through the chemical mixture of 8 main elements during the cement generation process.
The 8 main ‘elements’ present in cement are:
Lime (calcium oxide) 65-68%, Silica 17-20%, Alumina (aluminum oxide) 3-8%, Magnesia (magnesium oxide) 1-3%, Iron oxide 0.5-6%, Calcium sulphate 0.1-0.5%, Sulfur trioxide 1-3%, Alkaline 0-1%. These ingredients are ordinarily collected from limestone, clay, marl, shale, chalk, sand, bauxite, and iron ore.
How is cement made?
We will guide you into each step in the cement-making process from the minerals in the earth, to the cement powder that assists make concrete.
Digging for raw materials
The raw materials, essentially limestone, and clay, are derived from their victims by blasting or drilling using heavy mining machinery. The raw materials are transferred behind extraction and then brought to the crushers through dumpers.